- Published 30 Jan 2023
- Last Modified 23 Apr 2024
- 12 min
A Complete Guide to Industrial Workplace Safety

Reviewed by Pete Kendall, Technical Support Engineer (April 2021)
In every industry, workers' well-being and safety should be a top priority. This guide to health and safety in industry describes how to assess and prepare for key risks. It also sets out the specific responsibilities of both employers and employees. By implementing these guidelines, organisations can strive for optimal working conditions and reduce workplace incidents.
What is site safety?
Site safety is the practice of protecting workers, visitors, and equipment from hazards and risks in industrial workplaces, such as factories and construction sites. People working in factories and on construction sites are at significantly greater risk than those in comfortable offices, thanks to all those heavy objects, corrosive chemicals, forklift trucks, and production lines left running 24/7.
Site safety is important for preventing injuries, illnesses, fatalities, and property damage that can result from exposure to various hazards. It also helps reduce legal liabilities and costs associated with accidents and incidents. Additionally, prioritising site safety can enhance overall productivity, quality, and morale in industrial environments, as well as improve the reputation and image of the organisation.
Good practice in site safety involves drawing up a list of tight working procedures designed to control and minimise the risks posed by a particular location. Typical examples include:
- Full training
- The routine use of applicable safety wear (high visibility jackets, hard hats, etc.)
- Continuous communication between different teams
- Ongoing and routine inspection of potentially hazardous equipment
What are site safety rules?
Site safety rules are the guidelines and procedures that should be followed in industrial workplaces to prevent accidents and injuries. They are part of the construction safety plan, which outlines the objectives, roles, and responsibilities for ensuring a safe environment for all.Employers have a legal duty to protect the safety of employees, contractors and members of the public (for example, neighbours and visitors).A typical site safety rules template might include:
-
Wear relevant personal
protective equipment (PPE) at all times. On an average construction site, this is likely to mean, at the very least, a hard hat, safety boots and a high-vis jacket, but you may require additional items.
-
Keep things tidy. Tools and equipment that have not been properly stored, as well as general clutter, can lead to potentially serious falls and trips.
-
Don’t take unnecessary risks. Stay alert and avoid unsafe areas, such as directly beneath crane loads or heights without guardrails.
-
Report any problems or near misses immediately. This will allow swift remedial action to be taken.
-
Read and follow all safety signs and risk assessments for specific activities. Be generous with the display of construction site safety boards: keep everyone on their toes.
-
Never start work on a new site without a site-specific induction, setting out the hazards unique to that location.
-
Never try to improvise repairs or temporary fixes for faulty equipment or make unauthorised changes to a workspace (such as removing guardrails or handguards). The risks are obvious.
-
Be prepared: start compiling a building site health and safety checklist as soon as you know a particular job needs to be done. See below for more on construction site safety assessments.
-
Adhere to machinery safety instructions and use the appropriate tools and equipment for each task. Do not operate any machinery or equipment without proper training and authorisation.
-
Obtain permission before entering any restricted areas, such as confined spaces, excavations, or scaffolds. Follow the specific safety rules and precautions for those areas.
-
Refrain from substance use, such as alcohol or drugs, while on site. They can impair your judgement, coordination, and reaction time, putting yourself and others at risk.
-
Avoid disruptive behaviours, such as horseplay, fighting, or harassment, while on site. They can distract, provoke, or offend others, leading to conflicts, accidents, or injuries.
Site safety rules for contractors have a slightly different focus because they are new to your business and unfamiliar with your particular working practices. Unfamiliarity brings risks. As with employees, contractors have to behave responsibly and not place themselves in unnecessary danger.
/IDEAS%20and%20ADVICES/Safety%20Boots/Workplace%20Hazards%20and%20Safety%20Standards.jpg)
Site safety and risk assessments
Site safety assessments are the processes of identifying, evaluating, and managing hazards in industrial workplaces, such as factories and construction sites. They are essential for ensuring the health and safety of workers, visitors, and the public, as well as complying with legal and ethical obligations. Assessments will have some general elements that apply to all sites – but the specific combination of risks will often be unique to each location. If five or more employees are working on a particular site, your safety assessment must be written down. However, this is good practice even if there are fewer because it will help everyone keep track of their responsibilities. Site safety assessments begin right at the start, while the project is still in its planning stages, and continue throughout the project lifecycle.
Site safety assessments start with a risk assessment, which is a systematic process of pinpointing hazards, such as fire, electricity, chemicals, and noise, that may cause harm or damage. It also involves estimating the likelihood and severity of each hazard, and identifying who is most at risk from them. The risk assessment then informs the implementation of safety measures, which are the actions taken to eliminate or reduce the risks. Safety measures may include engineering controls, such as barriers or ventilation, administrative controls, such as policies or training, or PPE, such as gloves or helmets.
A site safety checklist template could include:
A list of the specific hazards – for example, heights, heavy loads, vehicles, and dangerous chemicals. A list identifying who is most at risk from each issue – particular employees? Members of the public? On-site contractors? An assessment of the urgency of each hazard – which are the most in need of attention? Discuss these with your team and possibly the local emergency services, too. Write down your conclusions, as well as the plans you have formulated to address each risk in a site-specific safety plan. Regularly review your assessment and change your plans as the project progresses.
Certain dangers – for example, chemicals, working at height, or loud noise – may require individual assessments.
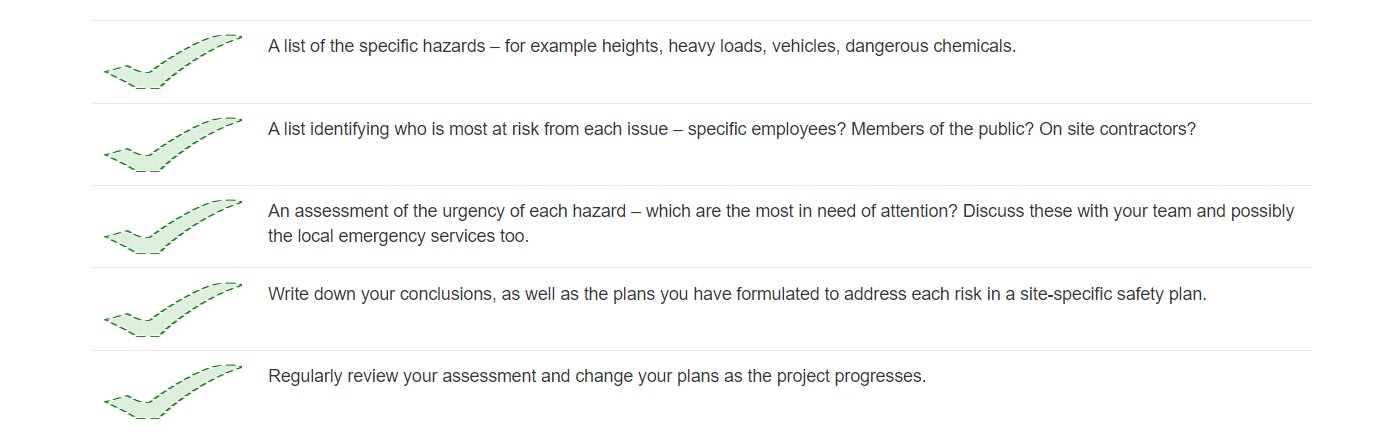
Common Hazards in Industrial Workplaces
Industrial workplaces pose various hazards that can cause injuries, illnesses, and deaths to workers and visitors. Some of the common ones include:
- Fires and explosions: Flammable materials, faulty wiring, gas leaks, and sparks can create fire and explosion risks in industrial settings.
- Electrical faults: Electrical equipment, cables, and power sources can cause electric shocks, burns, and fires.
- Chemical exposure: Toxic substances, corrosive materials, and hazardous waste can result in skin irritation, respiratory problems, poisoning, and cancer.
- Noise levels: Loud noise can cause hearing loss, stress, and fatigue.
- Ergonomic issues: Poor posture, repetitive motion, and lack of support can bring about musculoskeletal disorders, such as back pain, neck pain, and carpal tunnel syndrome.
- Biological agents: Infectious agents, such as bacteria, viruses, fungi, and parasites can cause diseases such as COVID-19, tuberculosis, and anthrax.
- Psychological stressors: High workload, low morale, conflict resolution, and coping skills can induce anxiety, depression, and burnout.
Site Safety Equipments
Working at height
Fall arrest harnesses are used to secure workers engaged in activities in high areas. If they slip or lose their footing, the tether will break their fall.
Tethered tools
A range of tethering equipment, including lanyards, karabiners, anchor points and blocks, can be used to prevent tools and equipment from falling from high points. Not only are such tools likely to be seriously damaged, but they also pose a clear risk to infrastructure and anyone passing below.
Spill control
Spill control equipment, which includes trays, bags and mats, is designed to provide a safe way for workers to clean up and dispose of potentially hazardous liquids.
First aid
Easily accessible first aid kits are a must for any construction site, as is training in the basics for at least some employees.
Fire alarms
A wide range of fire alarm accessories make it easy for construction companies to adapt their alarms to the specifics of each site.
Security
Factories and construction sites can be hard to secure, and some make tempting targets for thieves in search of equipment and raw materials that could be sold. Cut your risk with the wide range of customisable security alarms, switches, locks and bolts available.
Safety lockouts
Safety lockout equipment ensures that machines and power points in need of repair or maintenance are fully shut down, thereby preventing potentially serious shocks.
Floor marking tape
Floor marking tape and paint are used to provide quick visual guidance to workers and visitors, minimising health and safety risks.
Safety barriers
Safety barriers can play an important role in risk management on most construction sites, especially in areas where hazardous equipment or chemicals are stored.
Slip and trips
Anti-slip floor mats can save lives – install them in all high areas of your site where falls could occur.
Site safety signs
Safety signage requirements must be met on construction and building sites. Install clear hazard warnings in appropriate locations and health and safety information signs in common areas and on doors.
Site safety cards can be used to secure access to particularly hazardous areas.
How to improve industrial and construction site safety
Responsible industrial and construction site health and safety planning requires effort and can be costly, but it will certainly cost your business a lot less than a serious accident! Save lives and save your business.
Industrial workplaces can improve site safety by implementing a clear safety policy covering roles, rules, and reporting protocols. Consulting workers and stakeholders in safety planning encourages engagement and feedback. Regular safety training ensures awareness of hazards and procedures. Ongoing safety inspections promptly identify and rectify issues. Lastly, promoting a positive safety culture that rewards safe practices and discourages negligence is crucial. Some of the specific measures that can be taken to improve site safety are:
- Train employees required to lift and move heavy objects on how to do it safely, without injuring themselves.
- Look into noise insulation. Loud noises experienced over an extended period of time can cause hearing loss, high blood pressure, stress and headaches. Anything over 85 decibels should be a cause for concern. Ear protection, screens, acoustic barriers and equipment adjustment can all make a big difference.
- Slips and trips are one of the most common causes of injury on construction sites, injuring thousands every year. Everyone on site should keep a careful eye out for slippery or uneven surfaces, discarded objects, and trailing cables.
- If the construction site contains higher areas, be sure to install proper harnesses, guardrails or similar equipment in the vicinity, and be strict with procedures and training. Falls are one of the most common causes of fatal accidents in the construction industry.
- Monitor air quality and provide adequate ventilation. Dust is a significant health hazard on construction sites, so be sure to look at extraction systems, containment areas and breathing masks where necessary. Exhaust fumes can also be a significant risk to health on some sites, so consider on-site vehicles with catalytic and particulate converters. The overuse of gas heaters during the colder months increases the risk of poisoning.
- Monitor equipment regularly – especially portable equipment, which is especially prone to damage and mechanical failure.
Responsibilities of Employers and Employees in Ensuring Workplace Safety
Workplace safety is a joint obligation between employers and employees. Both must protect themselves and others from occupational hazards, adhering to legal and ethical standards. Fulfilling these duties fosters a safe and healthy work environment for all.
Employers' Responsibilities:
- Provide a safe work environment complying with safety laws and standards.
- Supply adequate safety equipment and offer comprehensive training to employees.
- Develop and update safety plans addressing specific risks and hazards.
- Consult with workers on safety matters and promptly address concerns or issues.
Employees' Responsibilities:
- Follow safety protocols and procedures relevant to their work activities.
- Wear PPE correctly and report hazards or incidents promptly.
- Participate in safety training and education to enhance awareness and skills.
- Support a safety-conscious culture and assist colleagues in complying with safety measures.