- Published 12 Jan 2023
- Last Modified 24 Apr 2024
- 8 min
A Complete Guide to Machine Safety
Useful guides to help you get the most from your equipment, applications and projects

What is Machine Safety?
Machine safety involves implementing practices, procedures, and technologies to shield workers from hazards posed by industrial machinery. Machines pose risks in factories and industrial settings such as sharp edges, clamps, and hot surfaces. Operational precautions, including physical guarding and warning signs, are crucial for safety. Additionally, machinery safety systems utilising switches and sensors help monitor operator-machine interactions, reducing risks when physical guarding is challenging.
Why is Machine Safety Important?
Machine safety is vital to prevent injuries and accidents in industrial settings, where machinery poses diverse risks to operators and workers. Risks associated with industrial machinery include cuts, burns, crushing injuries, limb entanglement, concussions, and wounds from moving parts or ejected objects. Operating machines safely is paramount, as poorly maintained equipment is more prone to hazardous breakdowns and power failures. Regular risk assessments and proper training for machine operators are essential measures to ensure safety.
What are the Best Machine Safety Products?
Let’s take a look at the key products that can be integrated into machinery or production lines to help ensure the health and safety of your employees:
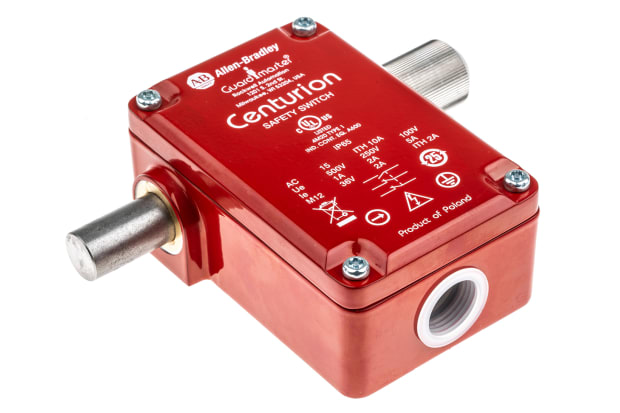
Safety Door and Interlock Switches
Safety-rated door switches, also known as interlock switches, are used to prevent or permit access to hazardous machinery, which has been protected by guarding or gates/safety doors: they do so by activating or cutting off the electrical current in particular circumstances and locking the barrier. For example, if key guarding has been opened, the current will be switched off.
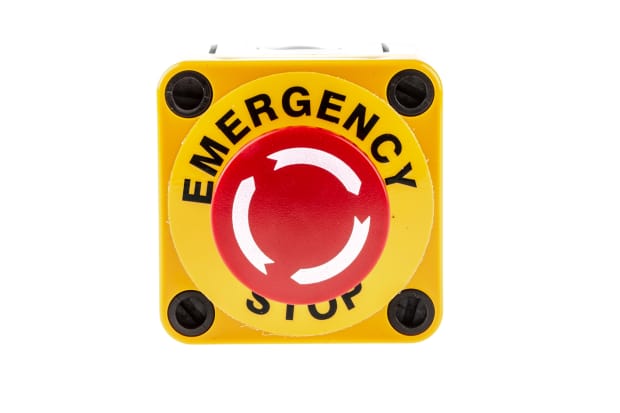
Emergency Stop Buttons
Emergency stop push buttons, also known as e-stops or kill switches, are fail-safe mechanisms that allow machinery to be immediately switched off in the event of an accident or other serious incident.
E-stops should be clearly marked and easily accessible, but not so accessible that they could be accidentally activated. They are available in three models: push-pull, key release and twist release.
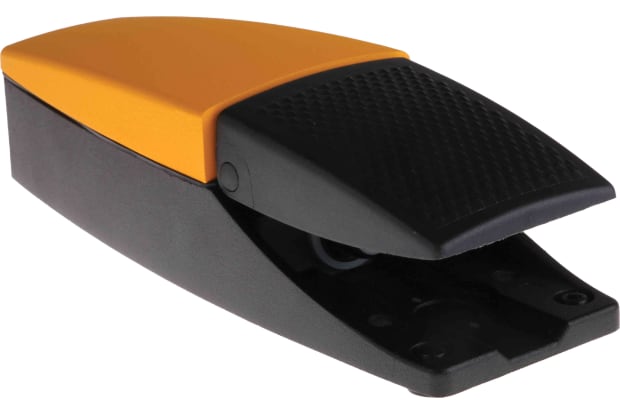
Foot Switches
Foot switches are a control mechanism typically used with larger machinery as a safer alternative to hand switches. Varying foot pressure activates or deactivates electrical circuits within the switch.
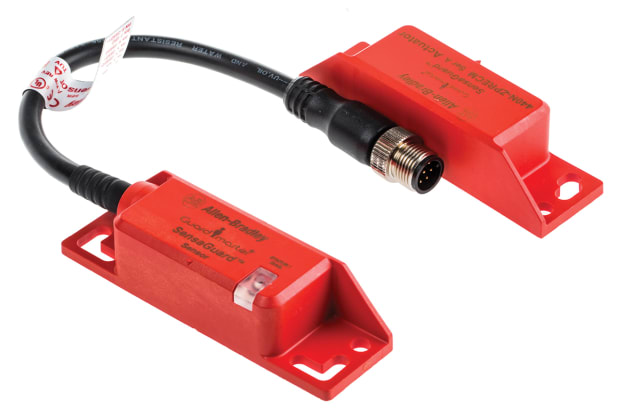
Non-Contact Safety Switches
Non-contact safety switches are designed to quickly switch off dangerous machinery and prevent injuries. They operate via transponders, inductors, or magnets and are typically hard-wearing, requiring little maintenance.
Safety relays
Safety relays detect electrical and mechanical faults in machinery, available in single or multiple-function models, with the latter being easier to install. Once an issue is identified, they activate safety measures like pausing machinery, initiating emergency stops, or cutting off electrical current. They often work alongside light barriers and safety mats to enhance worker safety and prevent breakdowns.
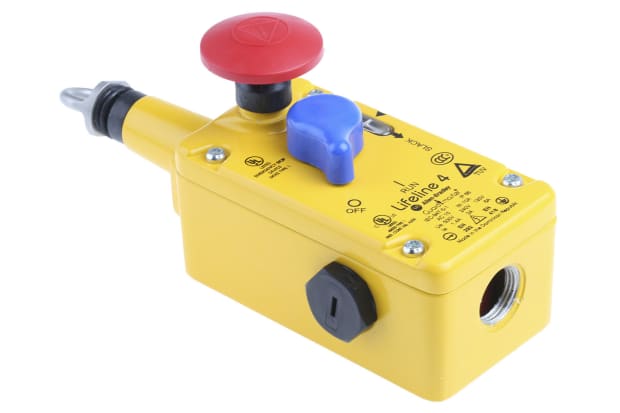
Grab wire switches
Also known as rope pull switches, grab wire switches provide an emergency stop function which is initiated by pulling on a wire, cord or rope.
They are typically used where a conventional emergency stop button would be awkward to access or inaccessible.
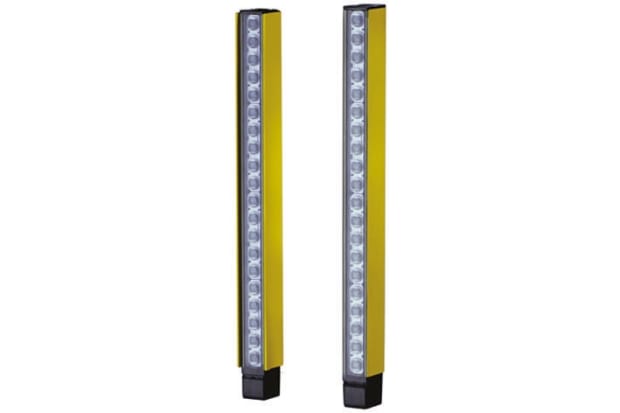
Safety light barriers
Also known as safety light curtains or safety light screens, these optoelectronic devices detect the presence of objects within certain areas and initiate an emergency shutdown of hazardous machinery when such detection occurs. They are designed to prevent injuries to workers who have gotten too close to the machines in question and are, therefore, at risk of injury.
They are available in a variety of sizes with different scanning capabilities and strengths.
Two hand switches
Safety two hand control switches prevent the activation of especially hazardous industrial machinery (for example, metalworking or printing machines) until both the operator’s hands are in place on the switch. This reduces the risk of accidental activation and injury.
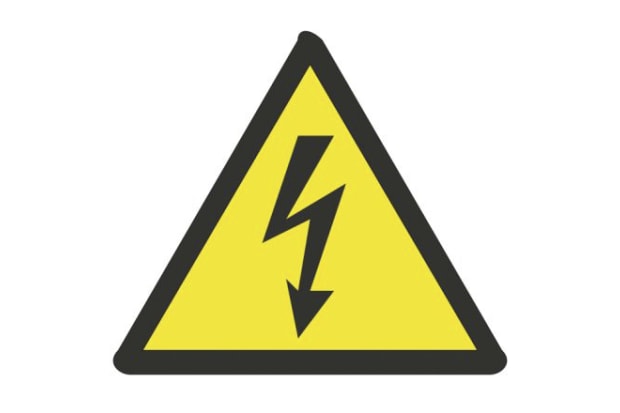
Machine safety signs
Machine safety signs provide an important component of health and safety planning, reducing accident risks by offering visual cues to mechanical hazards in key areas like machine shops and factories. Similar to road signs, they should be eye-catching and easily understood, and bold colours should be used to convey urgency.
Machine Safety Guidelines in the Workplace
While industrial machinery varies in function, safety principles remain consistent across lathe machines, grinding machines, presses, and packaging machines.
- It is essential to read the operating manual of any new machine carefully, even if you are already familiar with the basics. Always follow the instructions given. For more detailed guidance, refer to the handbook on guarding and operation of machinery provided by the HK Labour Department.
- Always wear machine-appropriate personal protection equipment (PPE). Closed-toe shoes protect your feet from impact and falling items and also reduce the risk of slips. Full wrap goggles shield your eyes from debris that may escape the guarding. Cut-resistant gloves can ward off injuries caused by exposure to sharp edges and blades. Read our guide to PPE here.
- Only operate machinery for which you have received full training.
- Visually assess the machinery and its fixtures and fittings before use, looking for any potential problems.
- Tie back loose clothing and hair and remove any jewellery to avoid the risk of entanglement.
- Ensure that there are no slipping or tripping hazards in the vicinity.
- Ensure you know the location of the emergency stop (e-stop) button if one is present and make sure you can access it immediately if needed.
- Establish clear lockout procedures and install barriers as appropriate, enabling the complete cessation of electrical current in emergencies or for maintenance. Presence-detecting light curtains will induce an emergency shutdown if they detect limbs in hazardous areas.
- Make sure appropriate guarding (shielding) is securely installed to protect operators and critical parts of the machinery itself from flying debris, sparks, moving parts, or entanglement hazards. Cabling should also be appropriately guarded. Only use guarding that is free from its own hazards – e.g., sharp edges. Always switch off machinery when stepping away from it.
- Fit easy-to-understand safety warning signs in visible locations for the benefit of anybody in the vicinity of the machine.
- Ensure that a well-thought-through cleaning and maintenance system is in place so that workers involved in such tasks are not exposed to unnecessary risks.
- Only fully trained technicians should conduct repairs and modifications.
Machine Guarding Safety Guidelines
- Never remove or tamper with machine guarding. If the shielding is worn or is coming loose, it should be repaired or replaced as soon as possible, not removed. Don’t run the risk of serious injury.
- Guarding repair or replacement should only take place during properly organised machinery maintenance.
- Never be tempted to bypass guarding and barriers, even to dislodge jammed items or conduct very small tasks: this is a regular cause of accidents.
- Guarding and barriers are not replacements for PPE when operating hazardous equipment.
- Proper training is vital to risk management. A machine operator who is aware of the key risks is much less likely to injure themselves.
- Always be aware of your surroundings when operating factory machinery. Notice if things don’t look or sound right. Surprises cause accidents.
- Don’t distract machine operators unless it is really necessary – a loss of attention could have serious consequences.
- Maintain regular maintenance schedules. Don’t skip scheduled checks: it’s far better to catch mechanical issues or developing faults before they cause an accident. Replace filters, sharpen blades and lubricate parts as necessary to cut the risk of breakdowns and overheating.
Frequently Asked Questions (FAQs)
Popular Machine Safety Brands
Schneider Electric
Schneider Electric is a trusted name in industrial automation and safety. With a focus on innovation and reliability, Schneider Electric offers a variety of safety products, including safety controllers, emergency stop buttons, and safety sensors, to enhance machine safety in diverse industrial settings.